Guy Norris/LOS ANGELES
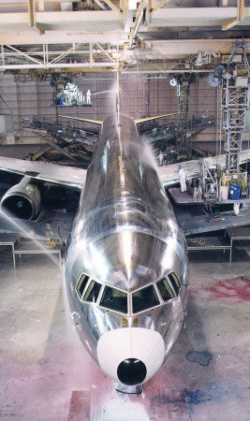
Boeing's big twinjet strategy takes another important step forward on 26 August when the 767-400ER is officially rolled out of the company's Everett assembly site in Washington. Appropriately dubbed "Stretch 2000", the programme promises to provide Boeing with an important new long-range asset in its war with the Airbus A330, as well as a vital injection of new life to sustain the 767 well into the new century.
Anyone seeing the 61.4m (201ft)-long aircraft emerge for the first time could be forgiven for experiencing a certain déjà vu. Not only is the -400ER a mere 3.6m shorter than the 777-200, but almost exactly 10 years ago, a similar "767-X" design was being proposed to airlines. This soon evolved into the all-new 777, and for a while the stretched 767 plans were shelved.
The seeds of the -400ER did not lay dormant for long, however, and sprang to life in late 1995 in response to two main stimulae - the go-ahead of the intercontinental range A330-200 and the emergence of a Lockheed TriStar replacement plan from Delta Air Lines.
First news of the 767-400X, as it was known in its study phase, was officially revealed at the 1995 Dubai air show, where the design exhibited the classic hallmarks of a Boeing stretch. It was expected to involve a 6.3m fuselage extension to create space for 15-20% more seats, 25% more lower deck volume and provide up to 10% lower seat kilometre costs than those of the 767-300. This last point was particularly important because Airbus was pushing several perceived advantages of the 256-passenger A330-200 over the older twinjet, one of them being direct operating costs 9% lower than those of the -300ER.
Delta's TriStar replacement competition therefore provided the expected battleground for yet another Airbus versus Boeing fight. Airbus pushed hard to get Delta aboard the A330-200 as part of a wider fleet deal involving widebodies and narrowbodies. Boeing was equally desperate for victory, as much to keep Airbus from gaining a foothold in Delta territory as to launch the strategically vital 767-400X.
Raised stakes
Raising the stakes substantially, the Boeing board authorised the provisional launch of the -400X in January 1997. The gamble was rewarded with a launch order from Delta the following March, when the Atlanta-based carrier announced plans to take 21 767-400ERs between May 2000 and 2001. It also announced options on 24 and a further 25 "rolling" options as part of a wider fleet deal which included Next Generation 737s, 757-200s, 767-300ERs and 777s. The programme was launched - now all Boeing had to do was build the aircraft.
Like so many other "simple" stretches, the 767-400ER quickly evolved into a more complex programme. While striving for the lower cost and improved production efficiencies of a minimum change design, Boeing accepted that the promised performance of the stretch could not be achieved without several fundamental structural, system and even aerodynamic changes.
The fuselage structure was strengthened to accommodate the greater bending moments of the longer body. It was stretched with a 3.4m forward plug added to the Section 42, and a new 3m section added aft of the wing-fuselage join. The revised design also includes modified fuselage panels, the assembly of which employs the Dassault/IBM CATIA digital design architecture developed originally for the 777 programme. About 80% of the -400ER was defined digitally.
To save up to 270kg (600lb) per aircraft in weight and reduce complexity, the fuselage also incorporates a stringerless window belt. The window shapes themselves are based on the low-stress elliptical design used in the 777 rather than the late 1970s-era rectangular shape used on existing aircraft.
Floor grid raceways
Major structural changes inside the fuselage include a revised floor grid structure with channels, or "raceways", built into the upper surfaces of the floor beams. These are aligned to accommodate the greater volume of wiring and cables that comes with the more sophisticated in-flight entertainment (IFE) systems, and replace the holes through which this wiring was traditionally routed. The beams also support seat tracks that are stressed to hold the seats while withstanding 16g loads.
The interior of the Section 48 tail cone is also changed to house the larger, more powerful AlliedSignal 331-400 auxiliary power unit (APU). Sized to provide up to 120kVA, rather than the 90kVA generated by the original 767-200/300 APU, the newer unit is based on a mix of technology developed for the 777 and Airbus A340 designs and can meet the higher power and air flow demands of the larger cabin. Higher capacity Hamilton Sundstrand air-cycle air conditioning systems, almost identical to those used in the 777, are used to provide a fresh air flow rate one-third higher than that of the -300ER.
The tail cone also houses a revised tail skid that builds on designs developed for the 777-300 and 757-300, but which differs from the 767-300's pneumatically actuated, hydraulic oleo design. The -400ER's hydraulically actuated unit contains a crushable cartridge that is designed to absorb the impact of a tail scrape with the runway on rotation or landing. The cartridge is replaceable and easily changed out, says Boeing, which adds: "The increased rotation capability achieved by the new tail skid arrangement on the -400ER improves take-off performance and can increase payload [out of obstacle-limited airports] by as much as 1,000lb. In addition, the lower profile of the revised tail skid design adds margin to avoid possible tail skid contact on landing." The move to the crushable cartridge allowed a gain of 0.2í in rotation angle margin.
A major design element of the -400ER is the main undercarriage, which was lengthened to maintain the existing rotation margin with the longer body. Significant changes were also planned to strengthen the structure to cope with the maximum take-off weight (MTOW) of 204,120kg, an increase of 17,240kg from the -300's MTOW. The resulting gear is 1,360kg heavier and 46cm (18in) taller than its predecessor, but has been designed to fit into the same wheel well with the minimum of change.
The wheels, tyres and brakes are identical to those of the 777, resulting in the use of 127cm radial tyres, compared with the 117cm-diameter bias-ply tyres on the -300. Hydraulic lines and the wing-mounted trunnion were shifted to ensure a snug fit for the gear, which is retracted with a more powerful air drive unit to compensate for the unit's greater weight. By ensuring that retraction time matches that of the -300, Boeing has also managed to add up to 1,270kg of payload out of obstacle-limited runways.
Changes to the wheel bay configuration involved moving a vertical beam on the rear spar - which forms the forward bulkhead - to the aft side of the panel. Even the change to the radial tyres, which explode in a different way to bias ply tyres, meant several systems had to be re-routed and redistributed to satisfy latest safety requirements.
The trunnion is shifted 25cm outboard and 10cm downward, a change that is only faintly visible externally thanks to a small aerodynamic blister at the forward end of the adjacent flap track housing. The new trunnion does not have the conventional cross-bolt - one of several design alterations to reduce corrosion. Others include plated bushing bores and an improved chip-resistant finish. The nose gear is essentially unchanged from previous 767 units, other than local strengthening to cope with the higher operating weights and the modified compression damping.
Cylinders forged
The first outer cylinders of the main gear for the -400ER were forged in June last year by Aubert et Duval in Les Ancizes, France, before shipment to BFGoodrich in Cleveland, Ohio, for finishing and final assembly. Another European forging company, Bohler Schmiedetechnik of Kapfenberg, Austria, provides medium-size, high-strength steel and titanium-alloy forgings for the main landing gear, torsion links, side struts, lower drag struts and spindles.
Because of its overall importance and the amount of changes involved, the -400ER gear became one of the major pacing items for the whole programme. "If we had used our conventional flow of manufacturing approach, we would have been about nine months too late, so getting here was a major accomplishment," says Mark Simpson, engineering co-leader of the landing gear integrated product team (IPT). "In a more typical development phase, we have 33 months from first commitment to parts on dock. We have managed to reduce that to 24 months for this."
A lot of time was shaved off normal business practices by using the CATIA system. "When our finite element analysis showed we needed to make a small change on the gear which would affect the forging, we created a new solid definition of the area on the computer and transmitted it to France," says Simpson.
"That was sent at three in the afternoon Seattle time, and by 8.00 the next morning here, we received back the modified three-dimensional geometry for that part. By the end of that afternoon, we had analysed the changes and gave Aubert et Duval the go-ahead to make the new form. So we lost no time. By Friday afternoon, we had the numerically controlled machine tape modified, and by the middle of the next week we had another forging struck."
Simpson says previous exchanges and changes of this nature "would have taken weeks, maybe months, to resolve".
Another key structural change to the -400ER is its increased wing span. To meet the original mission objectives, Boeing planned to increase the span to 55.2m with a fairly straightforward extension and winglets. Relatively late in the design effort, windtunnel data revealed that the slender tip extension could be prone to high torsional loads which would require further strengthening of the outboard section. A novel alternative was found - a raked extension resembling a winglet that has been flattened out to lie flush with the wing.
Aerodynamic tests confirmed the benefits of the swept tip design, which has since been patented by Boeing. Not only was the overall cruise performance improved, but the span was reduced to 51.9m, making it only 4.3m longer than that of the -300. As with the 747-400, the span of the 767-400ER will increase slightly to 51.99m with a full fuel load. The tips are 2.34m long and are made of composites with an aluminium leading edge for erosion protection.
Despite the unusual shape, the raked extension requires little change to the basic wingtip area other than a revised leading edge slat position, and new wingtip and position lights on the aft end of Section 48. Boeing says the -400ER will also be capable of dispatch with the wingtip devices removed.
Extra design work was needed to reinforce the wingtip attachment area to take the added bending loads produced by the tip. Much of this was modelled at the final assembly stage, using stereolithography techniques. Larger scale changes were also made to the wing as a whole, including general strengthening of the wing box. The raked tip has a quarter-chord sweep of 56.9í compared with 31.5í for the rest of the wing. Aspect ratio increases to 9.27 and effective area is raised to 290.7m2 (3,130ft2). Despite the span extension, fuel volume remains the same as the -300ER at 91,377 litres (24,110USgal), although plans for adding tail fuel in the proposed -400ERX version could see overall take-off weight this increased by up to 4,540kg.
Powerful options
The -400ER uses the same baseline General Electric and Pratt & Whitney engines as the earlier 767 and 747-400 models, but has been launched with an optional thrust increase to 63,300lb (280kN) offered with the GE CF6-80C2B8F version. Boeing first looked at 65,000lb-thrust engines for the -400ER, but "the engine itself is limited by the torque transmitting capability of the main shaft, so 63,300lb is about as high as it can go without major changes", says propulsion IPT team leader Kurt Kraft.
The two main areas of change for the propulsion system involved increasing the pneumatic and electrical supply. "This aircraft needs more pneumatic supply, so we needed to get more air out of the engine as smartly as possible," says Kraft. "We went to an electronic digital bleed control system, which tailors the demand to the aircraft while minimising changes to the bleed system. The ducting is common, but we have new valves with the same pre-cooler."
Using experience gained on the 767 AWACS, Boeing also added a 120kVA integrated drive generator (IDG) to produce more electrical power. "We needed additional oil cooling for the IDG, so we went to a secondary fuel oil cooler on the engine itself," adds Kraft.
Strut changes were also needed to cope with the 30% higher dynamic gust loads predicted for the bigger fuselage. "That was the biggest driver, and it forced us to increase the size of the strut to wing shear pins," says Kraft. "We also thought we would have to change the nacelle and strut for a blade-out situation, but we were able to define this pretty clearly using finite element models."
The engine has a new rear mount forging made from Inconel. "We also changed the shape of the mount so that we were able to stay with the same forging," adds Kraft. "That really cut down on machining time and produced a significant cost improvement, even though it's a few pounds heavier." Overall, the propulsion system as configured for Delta weighs 165kg more per aircraft than the -300ER. With the basic -B7F1 engine, the system is about 143kg heavier per aircraft - about 79kg less than the target weight.
The -B8F incorporates "boltless" high-pressure turbine area improvements, which includes a change to the longer-lasting Rene R88DT alloy and a new inner stage seal. Although this is expected to bring a 0.25% fuel consumption penalty, the pay-off will be longer life and higher cooling flows, says Kraft. The same technology is also at the core of a proposed refanned CF6-80C2G2 version that GE plans to test for a possible thrust increase to 65,000-68,000lb. This would meet the requirement of the longer range -400ERX.
Changes have also been made to the high lift system because of the higher gross weight. These include improvements to the flap/slat electronic unit, a schedule change to the flap load relief system, strengthening of the inboard flaps and the addition of inboard aileron droop for higher lift at low speeds. Another flight control system-related change is the adoption of a single yaw damper/rudder ratio change stabiliser module) to replace the federated yaw damper, rudder ratio change and stabiliser modules.
"We have combined three into one single LRU [line replaceable unit]," says 767-400ER forward cab engineering leader Fred Mazzitelli. "It takes up less space and has all sorts of goodies associated with it, and we're looking to migrate it into the -300."
One of the biggest challenges was faced by the flightdeck upgrade team. Relatively late in the -400ER design evolution, December 1997, the airline advisory group convinced Boeing to adopt a 777-style flightdeck rather than retain the existing layout. This decision helped cement Boeing's move towards a common-look flightdeck across its entire product range, from the 717 to the 777, but it gave the IPT a hard task because it was already almost a year behind every other development group.
Flightdeck consistency
"We knew where we wanted to go - we just had to work out how to get there," says flightdeck upgrade IPT lead engineer Mike Messick. "At first we looked at maybe doing the 757-300 and 767-400 together. Then, because of the urgency, we went into the 767 straight away." Fortunately, the IPT was able to use a lot of technology and lessons learned from the recent 777 and 737 Next Generation programmes. Also, the decision was made to keep everything the same as the -300ER from the glareshield up to maintain as much procedural commonality with the current fleet as possible.
The biggest changes are in the instrument panel displays, control stand and aft aisle stand. The flightdeck is dominated by six large format, Rockwell Collins-made flat panel displays which are reconfigurable and multifunction capable. The instruments are driven by three display processor computers, any of which can drive the entire panel. Two data concentrator units take all the analogue signals and convert them into digital format for the display processors. The processors therefore provide more redundancy, and reliability, than the -300ER flight deck, as well as the capability to reconfigure display formats to suit individual airline requirements - a key point in the search for commonality.
For example, the main primary flight display and navigation display (PFD/ND) formats selected for the -400ER are available with different altimeter options. "Some airlines said they didn't want an EFIS [electronic flight instrument system] format, which has tape altimetry, so we came up with a second altimeter format," says Messick.
Optional software
The alternative round-dial altimetry may be chosen as part of optional on-board software. Both current -400ER customers, Delta and Continental, have selected the tape display option. Boeing also planned to have a mini-PFD standby display, but size restraints mean it will now have the altimeter and ASI from the -300ER and the attitude indicator from the Next Generation 737 instead.
Messick says the legacy subsystem architecture of the 767 prevents "this from being a clone of the 777", but he believes the growth capability within the design will allow commonality to increase with time. Currently this is restricted to areas such as landing gear and flight controls, but hydraulics and electrics could be added in the future, he says.
Confidence in growth is based partially on the pioneering use of a Collins-developed Ethernet databus for the avionics system. Although the system is still designed to operate point-to-point, it uses Ethernet protocols and "being beyond ARINC 629 level, provides enough throughput capacity for growth", adds Messick.
The aircraft is also provisioned for as many IFE options as possible from the start, "so regardless of supplier, we could accommodate a wide variety", says Mazzitelli. As a result, these are six video control cabinet locations on the main deck, as well as two below deck. Len Wright, who is responsible for seeing the aircraft through to initial production, adds: "Integration of the systems into the fuselage has been one of the most difficult things we've had to do. Making it so the IFE systems were not intrusive on the other systems was probably one of the biggest hurdles. The wire bundles are up to 5cm in diameter - there will be a huge amount of wiring on this aircraft."
Cabin development
The cabin represented an entire development effort in its own right, and derived much of its appearance and technology from the 777 architecture. Interior development IPT leader Doug Ackerman says: "All the airlines wanted something like a 777, and all were adamant about bin space - specifically roll-on bags." The redesigned bins can take roll-on bags longitudinally in the centre pivot bins and two transversely in the side bins. The cabin also has new 777-style, seat rack-mounted lavatories and integrated wall and seat-mounted LCD monitors, as well as numerous lighting and style changes to emphasise a feeling of spaciousness.
A section of the cabin is built into the first aircraft, VQ001, and will therefore be part of the nine-month flight test effort. This is due to involve three aircraft, the third of which will have a full-up interior for dedicated operability tests, some of which could involve flights to and from Alice Springs, Australia. First flight is set for late September or early October, and certification and first delivery to Delta is set for next May.
Source: Flight International