Paul Lewis/FORT WORTH
The tiltrotor concept is not new, dating back almost as far as the first helicopter. The first helicopter-to-aeroplane mode conversion was made in 1958, by the radial-powered Bell XV-3, but it would take another two decades of advances before the XV-15 could demonstrate that the tiltrotor was practical. Twenty years on, and with the Bell Boeing V-22 Osprey military transport in production, the tiltrotor has come of age.
For Bell, having championed tiltrotor technology for so long, its next major goal is to be first into the market with a civil development by mid-2002. Despite the withdrawal from the programme of its V-22 partner, Boeing, the Texas-based company recently reaffirmed its commitment to the newly redesignated BA609 by making it the focus of a new joint venture with Agusta of Italy.
While the V-22 is set to spark off a rewrite of the US Marine Corps' manual on amphibious warfare, its smaller stablemate promises to bring a whole new dimension to the world of general aviation. The BA609 will be capable of flying twice the speed and distance of a conventional rotary wing machine, while retaining the point-to-point advantage of a helicopter over fixed wing turboprop aircraft.
"A fixed wing aircraft that doesn't need a runway is really a nice characterisation," suggests Don Barbour, marketing executive director of the Bell/Agusta Aerospace joint venture.
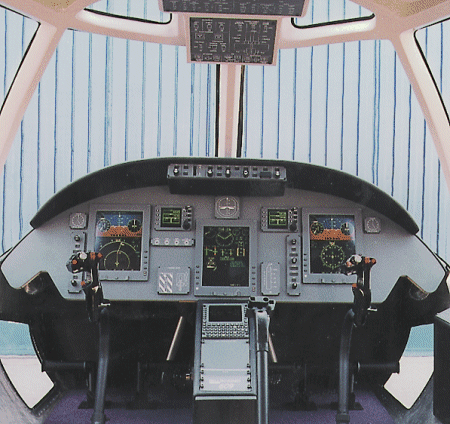
The BA609 characteristics mirror that of the V-22, with the engines rotated vertically to provide lift in the hover and swivelling horizontally to transfer lift to the wing and maximise forward thrust through the elimination of the characteristic rotor retreating blade stall.
Bell has selected the Pratt & Whitney Canada PT6C-67A engine, rated at 1,445kW (1,940shp) to drive the BA609's two 4.27m (14ft)-diameter three-blade proprotors. The engine is similar to that powering the Raytheon Beech 1900 commuter aircraft and the US armed forces' new T-6A Texan II trainer.
"Many of the tests that certified the engine for that use worked out great for us, because as a trainer it had to fly vertically. We said we could take all that vertical orientation and use it. The only thing we had to have them do in the vertical was start the engine, stop it and restart it, and they could do all that," recalls Barbour.
The BA609 will have a Rockwell Collins Pro Line 21glass cockpit configured for right-hand seat command, with the option to add a flight management system control display unit and health and usage monitoring system. The fly-by-wire flight control system has been designed with triple electrical/hydraulic redundancy.
Physical dimensions have been sized geometrically to fit the footprint of a medium helicopter. The BA609's 13.4m-long fuselage matches exactly the main rotor width of the Sikorsky S-76, while its width, at 18.3m tip-to-tip, is only marginally larger than the overall length of the Bell 412.
"We wanted to be sure the BA609 would fit existing infrastructure, such as heliports, hangar doors and the back of boats in certain cases," explains Barbour.
The BA609 fuselage and wing will be built of machined aluminium frames and ribs covered by a carbonfibre composite skin. Its 7,264kg (16,000lb) design maximum take-off weight will be less than one third that of the V-22. Internally, the tiltrotor's cylindrical cabin measures 1.47m side-to-side and 1.42m floor-to-ceiling. The 7.3m3 (258ft3) cabin is large enough to accommodate up to nine passengers in a standard utility configuration and six people in executive seating.
Bell has budgeted a 99.8kg weight allocation per passenger and two-man crew, including luggage, to produce an overall maximum payload of 2,497kg. The BA609's wing fuel tanks have been designed to support missions out to a maximum range of 1,387km (750nm) without reserves, at a cruise speed in fixed wing mode of 275kt (509km/h) at 84% engine rpm. The tiltrotor will have a service ceiling of 25,000ft (7,625m), with the cabin pressurised to 0.5bar (5.5lb/in2).
"We would like to be able to go to 1,000nm," says Barbour. "We've found some ways to put auxiliary fuel [455litres/120USgal] on the aircraft. We're looking into ways of making those a kit. The obvious places are in the baggage area or some external tanks under the wing."
The BA609's design has been primarily predicated on performing in five different market segments. As a Category A certification executive business aircraft or as a utility shuttle, Bell claims the tiltrotor will prove a faster point-to-point transport than either a helicopter over distances of at least 90km, or a fixed wing turboprop flying less than 900km.
As an offshore support vehicle, the BA609 on a normal day will be able to ferry up to nine passengers to an oil or gas rig up to 460km out to sea and, in the event of an engine failure on approach, it can abort in mid-mission and still return with a 30min reserve remaining. For hotter ISA +20°C conditions, such as in the Gulf of Mexico, its Cat A radius of operations reduces to 370km.
Bell estimates that the economic crossover point from an offshore support helicopter, such as a Eurocopter AS332L, to a tiltrotor is around 275km, beyond which it projects the BA609 will offer lower seat-kilometre costs. It will be equipped with emergency flotation bags on the two nacelles, which in tests up to sea state five have demonstrated they will keep the tiltrotor afloat if the cabin remains sealed.
A search-and-rescue (SAR) version, deployable from either shore or ship, is also being proposed to the US Coast Guard and other interested government agencies (see P35). It would be fitted with a winch, an enlarged 965mm sliding cabin door and be capable of accommodating up to six survivors. "It's an ideal combination that could substitute for both helicopters and aircraft used today by the Coast Guard," suggests Barbour.
The same modified cabin door would be incorporated into a planned emergency medical services (EMS) variant of the tiltrotor. As a critical care medical transport, the BA609 could accommodate two stretchers head to toe and three attendants. "We don't yet have an SAR user," says Barbour, "but three EMS operators indicate in their plans a role for the tiltrotor."
Another potential application being considered for the BA609 is as a lead-in trainer to the USMC's MV-22 tiltrotor transport, as well as possibly the US Special Operations Command's planned CV-22 and US Navy's HV-22 combat rescue versions. This would entail fitting the V-22's aeroplane-type throttle control lever (TCL) to the smaller tiltrotor, which Bell has elected to instead equip with a helicopter-style collective control.
Collective Decision
Bell's decision to opt for collective rather than a TCL is in part recognition that the BA609 is being viewed initially as a potential helicopter replacement and that many of the pilots now lining up to convert come from a rotary wing background. "These guys are used to managing their flights up and down-so we put a collective in there. The TCL will not be available commercially," says Barbour, but concedes "-this is a discussion point going forward".
Tiltrotor conversion will be controlled from the collective with a thumb action, with the position of the nacelle indicated on the instrument panel. The BA609 conversion between helicopter and fixed wing mode will be a staged transition taking 40s to complete. This compares to fewer than 20s for the XV-15 and as fast as 12s for the V-22.
"Stepped positions standardises the approach and departure profiles. It can be taught quite readily, slows down the conversion time and makes a very smooth transition for everybody aboard," says Barbour. Compared to a typical helicopter's 3í-6í angle of approach, the tiltrotor enjoys a wider range of 9í-12í and as high as 15í, but final landing profiles for optimum noise abatement are still being determined.
Tiltrotor pilot training and conversion syllabi have not yet been agreed with the US Federal Aviation Administration. Bell is planning for a skill-based qualification criterion rather than one predicated on flying hours. A planned new powered lift certificate will be granted most quickly to those pilots holding a combination of existing rotary, fixed and instrument licences.
"If you don't have a rotary wing background it will take you a little longer as you'll have to learn to hover and if you don't have a fixed-wing background it will also take a little longer to learn to fly higher and faster and deal with instrument flight rules [IFR] and icing conditions," explains Barbour.
The FAA is also planning to introduce a Federal Aviation Regulations Part 21.17B type certificate for the tiltrotor, representing a combination of existing helicopter and aircraft parts. This will include single pilot visual flight rules (VFR), two pilot VFR and two pilot IFR certification. First delivery of the BA609 is tentatively scheduled for mid-2002, but no firm order has been signed.
Fabrication of parts for the lead prototype is under way at Bell's Fort Worth plant, while Aerostructures of Nashville, Tennessee, will deliver the first BA609 fuselage in March 2000. The maiden flight of the first of four planned test vehicles is targeted for the end of 2000. The joint venture plans to produce up to 60 BA609s a year, about one-quarter of which will be assembled in Italy and the remainder at Bell's new tiltrotor plant at Amarillo, Texas.
Forty-one customers from 17 countries have committed to 72 BA609s, putting down payments of $100,000 per tiltrotor. Six months after the first prototype flies, Bell/Agusta have promised to provide firm pricing, warranty and direct operating cost information. Prospective buyers will be then required to sign a final purchase agreements and commit to a delivery position. "We know all of them," says Barbour. "I would characterise very few as speculative."
BA609 programme suppliers
* Pratt & Whitney CanadaPT6C-67A engines * Rockwell CollinsProLine 21 glass cockpit * Lear AstronicsFlight control computer * Messier DowtyLanding gear * Dowty AerospaceFlight control actuators * SimulaCrashworthy seats * SullyTransparencies * AerazurFuel Cell * HR TextronConversion actuators * TorayMaterials * HowmetPylon support casing * Aerostructurescockpit, cabin, aft fuselage * Fansteel WellmanDrive system casing * Haley IndustriesDrive system casing * Pacific ScientificGenerators and control units * Lucas AviationGenerators and control unitsSource: Flight International