Julian Moxon/Tel AVIV Cutaway/John Marsden and Tim Hall
The pressure is on at Israel Aircraft Industries (IAI) as its business aircraft division works to certificate its latest design by the late December deadline. The on-schedule maiden flight of the third prototype Galaxy on 23 September was a further boost to a programme that, after overcoming early production problems, has stuck rigidly to its schedule. The overriding aim now is to get this aircraft, the first built to series-production standard, to the all-important US National Business Aviation Association show at Las Vegas, Nevada, on 19-21 October, before which it must have built up a minimum 50h of flight time in Israel. "We are sure we can do it," says IAI Galaxy programme manager Zvi Genisher.
While technical development has proceeded almost without incident since it was launched in mid-1993, the Galaxy programme has been faced with production and financial problems which led to an 18-month delay in certification. The trouble began with the choice of Yakovlev as fuselage subcontractor. While its design ability was "very professional", according to IAI, the Russian company, which had only recently emerged from its Communist-era background, failed to meet quality and timescale requirements. "They managed to build a few parts, but we never saw a complete fuselage," says IAI business jet engineering manager Joshua Sher.
In the summer of 1995, therefore, responsibility for the fuselage was returned to IAI, which undertook a major effort to redraw the entire structure on to the Unigraphics three-dimensional computer-aided design system, along with the rest of the airframe. A bidders' conference was then held, leading to the selection of French company Sogerma as fuselage supplier, with IAI building the first five prototype examples, for which Sogerma was to provide the empennage, doors and tailcone. Following renegotiation of the deal when Henri-Paul Puel took over as president of Sogerma, all parties are now happy with the arrangements. "The quality of their work is really excellent," says Sher.
FINANCIAL SOLUTION
The next problem, lack of finance, resulted in a partnership being formed in February 1997 with the Pritzker group (owner of the Hyatt hotel chain). This led to the formation of Fort Worth, Texas-based Galaxy Aerospace, which is responsible for marketing and support for both the Galaxy and the existing Astra SPX business jet. IAI remains in charge of manufacturing and final assembly of the aircraft - and helps with sales from its Tel Aviv base.
The philosophy behind the Galaxy is straightforward: to offer business travellers a mid-sized, long-range business jet with the cabin dimensions, and therefore comfort, of a larger aircraft costing much more - hence the description of the Galaxy as a "super mid-size" business jet. Genisher explains: "Our intention is to give comfort equivalent to a 'heavy iron' business jet with the value and pricing of a mid-sized aircraft." The Galaxy price at $17 million for 1999 and $17.5 million for 2000 - more than the $10-12 million pricetag on current mid-sized jets, but considerably less than the $20-37 million cost of the top-of-the-range aircraft.
The market appears to be supporting the concept. While declining to reveal figures, Galaxy Aerospace says that orders to date amount to an 18-month backlog at the current planned production rate of eight aircraft in 1999 and 15 in 2000. "We expect the backlog to increase to two years and to be worth $350 million by certification," says Galaxy Aerospace president BrianBarents.
Genisher calls the design approach to the Galaxy a "prudent use of modern technology", combining an all-new design with the best of IAI's experience in more than 30 years of business jet activity. "We looked at the design on a case-by-case basis. Where we saw real cost benefits, we used the best technology available, but when we were undecided, we stayed with traditional techniques," he explains.
The Galaxy's heritage dates from 1967, when IAI introduced the Westwind, basically a modified version of the US-designed Rockwell Jet Commander fitted with new engines and avionics. This was followed by the Westwind II (with Garrett TFE731-3 turbofans, more fuel, winglets, and improved avionics and interior). Next came the Astra, certificated in 1985, incorporating a stretched Westwind II fuselage and introducing a new supercritical-section wing. The Astra SP followed, with digital (Collins Pro Line 2) avionics and a new interior. This led to the Astra SPX, certificated in 1996, with more powerful TFE731-40s, Pro Line 4 avionics, new interior and winglets. The six/nine-seat, 5,560km (2,950nm) range SPX is now being marketed by Galaxy Aerospace alongside the Galaxy. Sales have been increasing steadily since the US company took over both programmes.
ALL-NEW FUSELAGE
The Galaxy is based on an all-new "widebody" fuselage, attached to a strengthened Astra SPX wing with integrated winglets and modified high lift devices, powered by new 5,700lb (25.3kN) thrust Pratt &Whitney Canada PW306 turbofans, and with improved Pro Line 4 avionics and all-new interior.
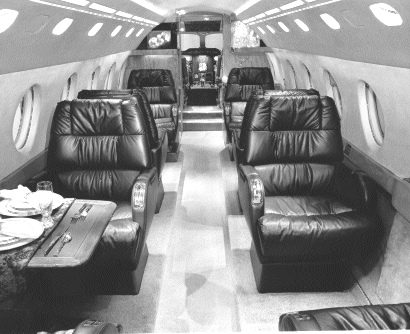
"We had a big debate about the size of the cabin when we were defining the fuselage cross-section," says programme manager Genisher. The decision to use the existing SPX wing imposed a limit on maximum size, but allowed for a fuselage large enough to accommodate three-abreast seating. The advantage of such an arrangement was that the cabin could be converted to an 18-seat "mini-commuter" layout - or any intermediate combination - if a corporate customer so desired. "We're getting strong interest in a configuration combining a four-passenger executive club area with a nine-passenger staff seating area," Genisher says . "The conversion can be done overnight, and we're finding that US companies in particular want to take advantage of the inherent flexibility."
That flexibility has been achieved by creating a wide, sunken, aisle into which modular "adaptors" can be fitted, allowing, for example, a wider floor - and hence seating area - on one side than on the other. This enables more seating configurations than with a fixed aisle, with the minimum of complexity, says IAI.
To maximise internal diameter and strength while minimising wall thickness, the main fuselage body is circular in cross-section - another departure for IAI, which retained the original Commander's oval section for the Astra range. "With the oval section you need more reinforcement," says Sher, "whereas, with the Galaxy, we were able to use a number of very thin fuselage frames to minimise wall thickness." The frames are just 5cm deep, and are attached to four main longerons, two near the top of the fuselage and two near the bottom. The design avoids the need for a large number of stringers, keeping it simple while providing ample structural stiffness. Sher points out that such a concept "-is only possible on an aircraft with a fuselage diameter of less than 2.54m-With larger types you have to have multiple stringers and frames to get adequate stiffness." To allow the seats to be located further outboard, all air conditioning tubing and electrical wiring is routed along the top of the cabin or under the floor, rather than at the sides below the windows.
As a result of a detailed cost/benefit analysis by IAI, the Galaxy's all-aluminium alloy airframe benefits from improved manufacturing technology in certain areas, which has brought a 20% reduction in parts count over that of the Astra. Most of the gain has been achieved by replacing items that were previously rivetted assemblies, such as the cockpit windshield frame, four main fuselage longerons and window cutouts, with components machined from solid.
At the rear, the fuselage is area ruled to minimise drag, the cross-section reducing dramatically at the engine inlet. Close attention has also been paid to the design of the engine pylons to reduce drag.
The Galaxy's supercritical wing has a leading-edge sweep of 34í on the inboard section, reducing to 25° outboard. The aerofoil section is an IAI design, perfected in its on-site windtunnels. Wing construction is traditional, featuring aluminium-alloy skin panels with integrally machined ribs. Both the Astra and Galaxy wings can be assembled in the same tool, eliminating the cost of designing and building a new one.
The main change from the Astra SPX wing is the introduction of Krueger flaps on the leading edges of the inboard section. These recover some of the field performance lost as a result of the Galaxy's higher wing loading. Slotted Fowler-type trailing-edge flaps are fitted and there are four spoiler/airbrake panels (instead of the Astra's two), the inboard pair of which act as lift dumpers. Leading-edge slats on the outboard wing section are linked to both the trailing-edge and Krueger flaps, and actuated electrically. Pneumatic de-icing boots are fitted to the wing leading edges, slats, Krueger flaps and slats and horizontal stabiliser leading edges.
In an arrangement used on several other aircraft, an extra fuel tank is carried between the rear cabin and the baggage compartment to give the Galaxy its all-important 6,700km range (at Mach 0.75 and a 15,170kg take-off weight). The location was driven by fan blade-off considerations that prohibit mounting the tank between the engines, but carried the inherent disadvantage that, because the baggage compartment is pressurised (an important requirement on business jets to avoid restrictions on luggage contents), a further two pressure bulkheads have to be added either side of the tank.
The aft-fuselage tank contributes to an overall fuel capacity of 6,496kg (14,250lb), the rest being carried in the wing and centre and forward fuselage tanks. Single-point pressure refuelling is provided, along with a gravity refuelling capability, and fuel transfer to maintain correct centre of gravity limits is automatic.
Following IAI practice of "-if it works, don't change it", the Galaxy's main landing gear is a scaled-up version of the Astra's, while the nosegear is taken from an existing commuter aircraft. Wheels and brakes are new, with anti-skid carbon brakes provided as standard. This saved development risk and cost, the only compromise being that the toilet floor had to be sloped upwards by around 3cm to make room for the larger gear when stowed.
The Galaxy primary flight control system features dual hydraulic actuators on the ailerons and elevators, and a manually operated rudder. The rudder and elevator mechanical backup linkage is by cable, unlike in the Astra, while the ailerons, elevators and rudder trim are linked to the cockpit by control rods. Flight testing, says Sher, has shown that the aircraft can be flown in mechanical backup mode in all conditions.
Hydraulic pressure at 207bar (3,000lb/in2) is supplied by two engine-driven pumps, with one electrically driven standby pump. All key systems remain operational with one engine inoperative, while, with total hydraulic power loss, the primary flight controls can be operated manually, the landing gear extended pneumatically and brakes and thrust reverser operated by an accumulator.
The PW306A turbofan was selected over the competing AlliedSignal/General Electric CFE738 in early 1994, after a detailed evaluation. The digitally controlled engine produces 5,700lb thrust, with growth to 6,000lb, and is flat rated to ISA +16°C. One of the reasons IAI cites for selection of the engine is that it can be started without the need for an auxiliary power unit (APU). Although the APU can still be used to start the engines, it therefore becomes a non-despatch item.
The AlliedSignal GTCP 36-150 APU is provided as standard in the aircraft and is flight rated to 40,000ft (12,200m). It is located on the rearmost fuselage frame and is accessed by removing the tailcone. "The APU is supplied as an operational flexibility feature," says Genisher. "It's basically a comfort item to maintain air conditioning and electrical power on the ground. Customers expect it these days."
The avionics suite is based around the Pro Line 4 system, with five 185mm multifunction displays. This consist of dual primary flight and multifunction displays, with the centre display being an engine indicating and crew alerting system (EICAS) - the first time that an IAI business jet has been so equipped. Besides displaying engine and system operating parameters, the EICAS has a trend monitoring and fault analysis capability - a feature considered essential for reducing maintenance time and cost. Genisher says that the EICAS is "-working beautifully - we're flying Version 3 now and we're on track for Version 4 in time for certification".
The Galaxy is also equipped with either a Universal or AlliedSignal Global flight management system certificated for global positioning system primary-means navigation. Dual communication, navigation and identification suites and a Collins TWR-850 weather radar with turbulence detection are provided, as are standby attitude, airspeed and altitude instruments.
Of the five prototypes in the test programme, two have been reserved for static and fatigue testing. At the time of writing, the static airframe had completed all limit load tests and two of the four ultimate load tests. Fatigue tests will begin in November. "We anticipate achieving 5,000 cycles by certification," says Sher. The damage-tolerant airframe is designed for an initial life of 20,000 flights or 36,000h.
Flight testing of the Galaxy has been virtually uneventful since the first of the three flying prototypes took to the air in December 1997. This was joined by the second in May 1998 and, by the time of the Farnborough air show - where the second aircraft was exhibited for the first time outside Israel - both aircraft had accumulated a total of 450h in 140 flights, heading for around 900h by certification in December. "We're following the curve we set out two years ago," says Genisher, who adds that such has been the pace of the programme, which has averaged 13 flights a week, each lasting around 3h, that the first aircraft took off with some of its systems untested. "We activated them gradually so that we could start earlier," he adds.
By the end of September, most of the main certification categories had been fully tested. Icing tests (to be carried out in Norway) are still to be done, but Genisher says it is "not a big deal"since the main affected component, the wing, is virtually unchanged from that of the Astra. Testing of the Collins autopilot was completed in mid-August, along with the reduced vertical separation minima capability.
Changes resulting from flight testing include the elimination of vortilons attached to the Krueger flaps to energise airflow "We found we didn't need them," says Genisher. The wing/fuselage fairing has been reshaped, and the angle to which the airbrakes are deployed increased from 35° to 45°. Adjustments continue to find the best relationship between the nosewheel steering tiller and rudder, and the usual attention is being paid to seals and gaps to reduce airflow noise. "Basically, this has been a virtually flawless programme," says Genisher. "The aircraft has been reliable from the start. We're delighted with progress, and I believe we'll make certification and deliver the first aircraft early next year as planned," he adds. The first aircraft will go to a Norwegian shipping company after interior completion at Galaxy Aerospace's facility in Fort Worth.
Barents says that the main competition is the forthcoming Raytheon Hawker Horizon ("it's not quite as big and it doesn't go as far"); the Dassault Falcon 2000 ("a lot more expensive"); and the Cessna Citation X ("a much smaller cabin and less range"). He adds that "-others may have super mid-sized business jets on the cards, but the fact is - we're here already".
GALAXY SPECIFICATIONS | |
Height | 6.53m |
Length | 18.97m |
Wingspan | 17.71m |
Wing area | 34.28m2 |
Cabin height | 1.91m |
Cabin width | 2.18m |
Cabin length | 7.44m |
Maximum ramp weight | 15,241kg |
Maximum take-off weight (MTOW) | 15,173kg |
Maximum landing weight | 12,474kg |
Maximum zero fuel weight | 10,433kg |
Basic operating weight | 8,414kg |
Useful load | 6,827kg |
Maximum payload | 2,019kg |
Usable fuel | 6,464kg |
Balanced field length (MTOW) | 1,841m |
Landing distance | 1,036m |
Typical cruise speed | 871km/h (470kt TAS/Mach 0.82) |
Vmo (sea level to 3,050m/10,000ft) | 574km/h |
Vmo (3,050m to 7,600m/20,000ft | 667km/h |
Mmo | Mach 0.85 |
Maximum range, NBAA/IFR | 6,706km |
Maximum altitude | 13,716m |
DIGITAL REVOLUTION
A"triumph in concurrent engineering" is how Unigraphics, designer of the Galaxy digital mockup, terms the achievement which has seen the entire aircraft defined electronically. Manufacture and assembly was carried out directly, using the digital mockup, resulting in a saving of about $2 million from the elimination of a wooden mockup and the absence of the change orders which used to dog aircraft programmes. A classic example of this was the early detection, during a test of the undercarriage kinematics, of the potential interference with the cabin floor. "This would have been difficult to detect even with the most elaborate physical mockup," says Sher. Tube routing was also defined using the system, and sent directly to the tube bending machine, again saving considerable time and money. A further advantage is that the entire Galaxy maintenance manual comes in a pack of CD-ROMs, vastly simplifying maintenance because of the interactive way in which information is presented.
Extensive use of computational fluid dynamics also played a vital part in establishing aerodynamic profiles for critical areas such as the cockpit, wing/fuselage interface and engine pylon. In the latter, IAI's own programme enabling computer visualisation of transonic airflow helped develop a double curvature solution that reduced the local Mach number to below 1.0, eliminating shock waves, and the resulting drag.
Source: Flight International