Development problems overcome, the C-130J is being prepared for entry into service
Michael Gerzanics/MARIETTA
Claiming 50 world records over two days earlier this year was more than just a demonstration of the C-130J's superiority over previous Hercules; it was an effort by Lockheed Martin to demonstrate to the world that the programme's well-publicised problems are in the past.
After substantial development delays, the company is preparing to deliver the first C-130Js to operational units of the UK Royal Air Force and Royal Australian Air Force (RAAF), launch customers for the private-venture programme. The first RAAF aircraft will be handed over at the end of this month and the C-130J will enter RAF service in November.
Lockheed Martin, meanwhile, has rebaselined the programme to write off higher than expected development costs and adjust to lower than anticipated production rates. The company has firm orders for 90 aircraft, about half of which have been built, but hopes to see production pick up again by 2002, when the US Air Force begins a planned 150-aircraft procurement. Lockheed Martin, meanwhile, has committed to cutting the C-130J's price by $10 million through lean manufacturing.
The company's original estimates were based on developing one USAF-standard configuration, but when the air force delayed its procurement plans, Lockheed Martin was forced to seek international launch customers. As a result, the company ended up developing at least five configurations simultaneously. This, coupled with unforeseen problems integrating and certificating the new avionics and propulsion system, led to the delays, Lockheed Martin says.
Flight International first evaluated the C-130J in December 1997 when Peter Henley flew an RAAF C-130J-30, a 4.57m (15ft) stretch of the basic aircraft. Since that flight, the C-130J has continued to evolve, receiving US Federal Aviation Administration certification in September last year. Because development was a private venture, civil certification was required in lieu of military qualification to guarantee airworthiness. The process proved more burdensome than the company expected.
One visible change to the C-130J since Henley's flight is the addition of a black rubber de-icing boot at the base of the vertical stabiliser. This had to be added after Lockheed Martin discovered, in the final stages of the certification test programme, that the J's ice accretion characteristics were not the same as those of previous Hercules. Icing detectors, co-located with the pitot probes on either side of the nose, allow the ice protection system to operate in an automatic mode, reducing crew workload.
Icing characteristics had changed for the same reason that the J's stall behaviour had changed, causing problems earlier in the certification programme - the different airflow from the new six-bladed propellers.
The Dowty R391 propellers, with their distinctive sickle-shaped composite blades, distinguish the C-130J from previous Hercules. They are driven by Rolls-Royce Allison AE2100D3 turboprops, flat rated at 3,500kW (4,700shp) at 39°C, and with dual-channel Lucas Aerospace full-authority digital engine control (FADEC) systems. This engine and propeller combination provides the J with up to 25% more thrust at sea level than a C-130H.
While the new engine/propeller combination improves performance, changes to the C-130's avionics and crew stations form the heart of the upgrade. Automated systems combine with a central mission computer and 1553B databus to make the J a true two-pilot aircraft. Digital avionics and dual embedded global positioning/inertial navigation systems have made the navigator redundant. Two wide field-of-view head-up displays (HUDs) and four 150 x 200mm liquid crystal head-down displays (HDDs) allow two-pilot operation.
Customised features
Certification complete, Lockheed Martin is developing features desired by various customers. One being developed for the US Air Force is the independent precision radar approach (IPRA) system. This gives the J a precision approach capability similar to an instrument landing system (ILS), wholly from onboard avionics.
I was able to observe flight testing and fly the C-130J during a 2h 50min sortie at Dobbins airbase, co-located with Lockheed Martin's Marietta, Georgia, facility. I was accompanied by chief experimental test pilot Lyle Schaefer and test pilot Bruce Remick. Additionally, two flight test engineers were onboard and two systems specialists performed loadmaster and crew chief duties throughout the flight.
We flew a standard length USAF C-130J. The aircraft had a zero fuel weight of 37,705kg (83,055lb), well under the maximum allowed 54,450kg. Just under 11,350kg of JP-8 fuel was loaded, compared to a maximum internal capacity of 19,870kg. Resulting ramp weight was about 49,000kg, well under the maximum take-off weight of 74,455kg. Except for a few flight test instruments, the aircraft was representative of those being delivered to the Air National Guard.
I accompanied Remick on a walk-round of the J. As it was a rather hot, 36°C day, and the auxiliary power unit (APU) was running, providing bleed air to the separate flightdeck and cargo compartment air-conditioning packs. Located in the left main gear sponson, the APU was noticeably louder than on most civil transports. Any discomfort from APU noise was quickly forgotten, however, once we entered the cool flightdeck. Lockheed Martin claims the cooling system has 25% more capacity than the unit in the H, and is more reliable.
As in previous C-130s, access to the aircraft is via steps on the left forward entry door, then up the flightdeck ladder to the left. What awaits at the top of the ladder is a mix of the familiar and the new. The two-way adjustable seat and four-point harness are standard C-130 and the positions of the yoke, rudder pedals and throttles will be familiar to the seasoned Hercules pilot. Everything else is quite different. The navigator's station has been removed, as have both the navigator's and flight engineer's seats. A centre third seat is available should mission requirements dictate.
The overhead panel contains controls for the J's major systems: electrical, pneumatic, fuel and air conditioning. The hydraulics, comprised of utility and flight control boost systems, are controlled from the right front instrument panel. Four engine-driven pumps, two apiece, power the 207 bar (3,000lb/in2) systems. The right engines provide boost for the flight controls, while those on the left power the utility system - a carryover from previous C-130s, which would seem to compromise combat survivability. While the aircraft can be flown with both systems inoperative, a pump on each wing might have been a more survivable solution.
The instrument panel and glareshield, while radically different from a standard C-130's, have changed little since Flight International last flew the J, but four HDDs are now LCDs. Replacing the original cathode ray tubes reduced avionics heat loading, while providing more readable and reliable displays. Flight directors (FDs), autopilots and radios are controlled via glareshield- mounted panels. While there are a number of conventional circuit breakers (CBs) on four side panels, there over 350 digital CBs. These are controlled through the communication/navigation/electronic circuit breaker panel at the centre of the glareshield. This de-clutters the cockpit, while the mission computers monitor and report their status to the crew.
Cockpit set-up
The test flight was conducted in two parts. The first consisted of seven IPRA test runs with Schaefer in the left seat and Remick in the right. I occupied the centre third seat and watched. Cockpit set-up and flight management initialisation seemed logical and straightforward.
The number three engine was started first by APU bleed air, after rotating its start switch on the overhead panel. At 12% NG (gas generator RPM) the engine lit off; at 65% NG the starter cut out, and the engine accelerated on its own to low-speed ground idle (72% NG). Peak measured gas temperature (MGT) was 633°C, with a limit of 807°C. The three remaining engines were started simultaneously. All four engines were at low- speed ground idle, a FADEC mode that reduces fuel flow and propeller RPM for ground operations, in less than 3min.
Before leaving the chocks, Schaefer checked operation of the dual stall warning/stick pusher system and control-yoke pilot override switch. After releasing the parking brake, the J was taxied at a comfortable speed. The APU was left running to provide electrical power, as engine generator operation is not assured at low speed ground idle. The pilot's nosewheel steering (NWS) wheel is standard C-130, providing ±65° of steering. There was no rudder pedal NWS actuation. Schaefer had no difficulty following taxiway lines as we proceeded to the active runway. Had the taxiways been slippery, differential thrust could have been used to maintain directional control.
Remick read the take-off checklist from a card, as electronic checklists are not incorporated in the J's flight management system. While awaiting take-off clearance the throttles were advanced to the flight idle position, and the propeller overspeed governors were checked. Not much else was required.
Between successive approaches Remick showed me some of the J's avionics capabilities. On the head-down navigation display (ND) he called up the traffic alert and collision avoidance system (TCAS) overlay - a rarity on military aircraft. Identical to commercial TCAS, it greatly enhanced our visual lookout in the congested airspace surrounding Atlanta. One shortcoming of TCAS, however, is the lack of altitude information on targets without encoding transponders. The skin paint air-to-air mode of the J's radar, which employs a relatively narrow pencil beam and displays only targets at or near our altitude, greatly enhanced our awareness of non-altitude-reporting TCAS targets.
Beam-sharpening radar mode
In addition to a normal ground mapping mode, the Northrop Grumman Modar 4000 radar has a Doppler beam-sharpening (DBS) mode which provides finer resolution of ground targets. The last time I had used a DBS ground mapping radar was as an F-16 pilot, and the J's resolution of a small civil airfield appeared to be on par with the F-16's. The radar cursor can be slewed by a button on each outboard yoke handle. A third cursor slew button is located on the centre console, enabling the centre third seat occupant to operate the radar.
After the last IPRA trial Schaefer set the aircraft up for a visual approach to runway 29 at Dobbins. The approach was flown at flaps at 100%, the J's normal setting.
While taxiing, Remick started the APU with a single switch throw on the overhead panel. It reached idle RPM in 20s; peak exhaust gas temperature (EGT) was 402°C, with a limit of 710°C. With the APU supplying electrical power, the engines were placed in the low-speed ground idle mode by pushing four buttons just aft of the throttles.
After the flight-test engineers had deplaned and the doors were closed, we taxied out for the second part of the flight. Schaefer and Remick demonstrated a maximum-effort short take-off on this calm day. The flaps were set at 50° and throttles advanced to the maximum power stop. Brakes were released once the engines had stabilised at full power. Acceleration of the 45,500kg aircraft was brisk, to say the least. The combined decision (V1) and rotation (Vr) speed of 94kt indicated airspeed was reached in less than 14s. The J leapt off the runway after a ground run of less than 460m (1,500ft).
Climb out was equally impressive. A 20° nose high attitude was needed to hold just above the takeoff safety speed (V2) of 103kt. The steep climb profile would enable the J to climb quickly beyond range of small-arms fire at or near the airfield perimeter. Once level at 5,000ft, Remick and I switched seats. In the right seat I came face-to-face with the J's most striking feature, the Flight Dynamics HUD. I adjusted my seat so I could read the symbology in all four corners of the display without moving my head.
Compared to the HUD in the F-16, I found it cluttered, but Remick pointed out the important cues for each phase of flight. Three levels of display de-clutter are selectable by a yoke-mounted button, a feature I found useful.
One reason for the complexity is the HUD's certification by the FAA as a primary flight display (PFD), an industry first. Most glass cockpits have a six-display set up: PFDs and NDs for each pilot and two for the engines and systems. The J's four displays, with two for the engines and systems, leaves only one for each pilot. Certificating the HUD as a PFD made the J a six-display aircraft, but undoubtedly lengthened the certification process.
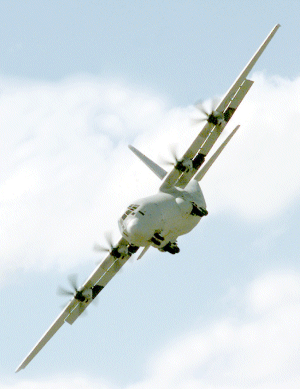
Power stop
As we headed west and started to climb, I jammed all four throttles forward to the maximum continuous power stop. The digitally controlled engines and propellers responded by accelerating rapidly without complaint. The "carefree" and linear engine response afforded by the FADEC should ease pilot workload during tactical manoeuvring, when aggressive throttle "chops" may be required to defeat an infrared-guided (IR) missile.
During the climb I gently manoeuvred the aircraft to get a feel for the conventional hydraulically boosted flight controls. In general the control forces were fairly light at lower airspeeds, below 150kt, and stiffened up at higher speeds. Lateral directional (roll and yaw) control was well harmonised, with the rudder being more effective at slower speed and ailerons predominating as we accelerated. Yaw control was slightly complicated by the effect of the propellers. From any trim condition, adding power necessitated the addition of right rudder; reductions required left rudder. Hercules pilots do this subconsciously, but I had to work at it.
The new engine/propeller combination, while improving performance, also caused problems early on. FAA regulations require that any wing drop in a stall be less than 20°. Stalls during the J's initial development, while generally benign, generated bank angles in excess of 20°. Several months were spent seeking an aerodynamic fix. Some worked at high power settings, others only at low power, but none at both. In the end Lockheed Martin settled on a stick pusher to provide reliable stall recovery characteristics at all power settings.
Once level at 7,500ft we set up to execute a clean straight ahead power-off stall. When we slowed to within 40kt of the 44,000kg's J's predicted stall speed, a caret labelled with an "S" appeared on the HUD airspeed display. Had the autothrottles been engaged, they would have advanced to maintain 1.2Vs (stall speed).
Slowing the J at 1kt/sec, an audible "Stall, Stall" was sounded, accompanied by the word "Stall" on both the HUD and PFD, at 109kt. Still holding back pressure on the yoke, the stick pusher actuated at 101kt. The yoke was pushed forward with about 27kg of force, and rapidly prevented the impending stall. Wings remained level throughout the recovery and the aircraft climbed out with the addition of power.
Take-off configuration stall
After the short climb back to 7,500ft, we set up for a take-off configuration stall. The undercarriage was lowered and flaps set to 50%. As I adjusted the power setting, the stall caret moved on the HUD airspeed display. While stall speed in jets is only slightly affected by power setting, the J's turboprops have a sizable affect on wing lift. All four engines were set to 1,220kW, a mid-range setting close to that specified by the FAA for this flight condition. The aural stall warning sounded at 84kt and the stick pusher actuated at 76kt. Again there was no wing drop and I was able to fly out of the stall easily.
While the aural and visual stall indications are adequate, I would have preferred a stick shaker as the primary indicator of an impending stall. RAF and RAAF C-130Js will have the optional stick shaker installed. The third and final stall was in the landing configuration. Flaps were selected to 100% with the gear still down and throttles were retarded to flight idle. Stall warning occurred at 81kt. This time, when the stick pusher actuated at 74kt, I held the yoke aft, showing it could be manually overridden.
Through the flight management system, Schaefer selected a "direct to" leg for our return to Dobbins. A full colour map was displayed on my HDD which depicted our flight route. Lateral steering guidance on the HUD was easy to follow as we started our recovery.
Like previous Hercules, the J does not have a yaw damper. As we descended at 230kt, I initiated a dutch roll with a gentle rudder doublet. The result was a well damped snakey response in yaw, with very little roll. Proper application of the rudder easily stopped the dutch roll in less than one cycle.
I continued the descent at flight idle, which gave a descent rate of 3,600ft/min (18.28m/s). A more rapid rate of descent could be possible if ground-range propeller angles were available in flight. Had the J been purely a military programme, that feature would have probably been available. But the FAA frowns on giving pilots that option, as misapplication could lead to loss of aircraft control. Software in the J's mission computer uses two radar altimeter and two weight-on-wheels signals to prohibit propeller settings below flight idle while airborne.
At about 1,000ft above ground level, I set up for some low altitude tactical manoeuvring. Once established at 230kt, total fuel flow was about 2,270kg/h. Being a light wing-loading aircraft, the J's ride was somewhat bumpy, but cockpit tasks could be accomplished with little difficulty.
The cockpit "greenhouse" provided excellent field of view above and to the rear of the aircraft. From the right seat I was able to see to the 4:30 clock position.
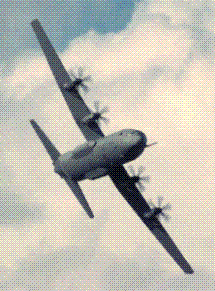
I next simulated a surface-to-air missile break by rapidly rolling to 60° bank. Once banked I pulled to just over 2g, well under the 3g limit for our configuration. The nose tracked smoothly across the horizon as we rapidly turned our tail away from the simulated threat.
Having survived the simulated missile attack, we set up for an ILS approach to Dobbins' runway 11. I followed the HUD steering cues to intercept and track the localiser inbound. Little pitch trim was required to maintain a level attitude when the flaps were extended to 50% and undercarriage lowered at 150kt. Flap extension from 50% to 100%, as we neared the glideslope, required about 5.5kg of aft stick force to maintain level flight.
Once the 3° glideslope was intercepted I used the HUD alone to fly the approach. Guidance was excellent, allowing me to track both localiser and glideslope accurately. The airspeed tape on the left side of the HUD allowed me to maintain airspeed manually to within ±3kt of the 118kt approach speed for the 43,585kg aircraft. At decision height, I smoothly advanced the throttles and initiated a go-around. As the flaps retracted from 100% to 50%, the pitch trimmed automatically nose down to help maintain the 10° climb out attitude.
Climbing turn
After the missed approach, a climbing left-hand turn was flown to a visual downwind leg for runway 29. The undercarriage was lowered on base leg for a touch and go landing. A 3° visual approach was flown at 127kt, about 10kt faster than the earlier 100° flap approach. Aircraft attitude was 4° nose down as we crossed the threshold at 50ft. I started the flare manoeuvre at 25ft and slowly retarded the throttles to flight idle. About 4.5-9kg of aft stick pressure was needed to attain a touchdown attitude of 1° nose high. The J settled gently to the runway about1,000 ft from the threshold.
After lowering the nosewheel to the runway, I advanced the throttles to maximum continuous power. Directional control in the 9kt quartering headwind was made easy by the effective rudder. At 120kt, I rotated to a 10° pitch attitude. Once airborne, I increased the pitch attitude to 20° nose high, to climb out at 125kt. We left the undercarriage extended for the rest of the flight to cool the brakes .
Once level at pattern altitude, Schaefer simulated an engine failure by retarding the number four throttle to flight idle. At 150kt, there was more than enough rudder trim available to trim out the resulting asymmetric thrust. To get a better feel for the rudder forces required, I set the rudder trim to neutral for this approach. The flaps were set to 100%. On final at 118kt about 27kg of rudder force was required to fly a co-ordinated approach. I brought the J to a stop 1,700ft from the touchdown point, without reverse thrust.
After a normal take-off, I turned the J over to Schaefer for a maximum effort full stop landing. Flaps were set to 100% and an approach speed of 96kt (1.15Vs) was set. Using the HUD as an approach aid, Schaefer flew a 3° glidepath to a touchdown slightly past the threshold. Using maximum reverse thrust and wheel braking, the J was stopped just short of the approach end arresting gear, only 1,550ft down the runway.
Setting world records for speed and altitude with tactical payloads, the C-130J has shown itself to be a marked improvement of an already capable design. While performance enhancements alone could justify the C-130J, the cockpit upgrade has been extremely successful. Dual mission computers, advanced displays and the databus architecture have replaced two crew members, while increasing mission capability. The C-130J appears ready to go to work.
Source: Flight International