An ambitious British bid to develop a pair of hybrid-electric, uncrewed freighters with payloads of up to 350t and using a new type of ultra-lightweight shipping container has broken cover.
Droneliner’s designs for the carbonfibre aircraft feature a basket of new and emerging technologies including ultra-high-bypass widebody engines, truss-braced wings, electrically-driven landing gear and a roll-on/roll-off cargo bay.
However, there are formidable regulatory challenges to overcome if an uncrewed cargo aircraft of this size is to be brought into service, not to mention the billions of dollars it will take to develop the jets.
Two variants of the Droneliner concept are proposed: the single-engined, 200t-payload DL200 and the larger 350t-payload DL350 twinjet. They will have respective maximum take-off weights of around 350t and 600t – roughly in line with the Boeing 777 Freighter and Antonov An-225.
While the enormous aircraft are the most eye-catching part of the project, their operation will only be enabled by the adoption of lightweight plastic/vinyl shipping containers in place of the ubiquitous metal versions.
At just 400kg (880lb) empty weight, the new containers would be an estimated four-fifths lighter than a standard 6m (20ft) metal container, but would have the same footprint and anchor points, making them significantly more versatile, the company argues. The DL200 would carry up to 40 units of the lightweight boxes across three decks, while the DL350 would accommodate up to 70.
Droneliner sees potential for the aircraft and the lightweight container combination to have the same effect on the air freight industry as the original shipping container had on sea freight.
By doing away with the need to break down large consignments to fit them in aircraft-specific LD-standard containers, known in the industry as break-bulk, Droneliner argues that huge cost and efficiency gains can be realised, enabling next-day factory-to-customer services.
Work on the freighter pair is at a preliminary stage but initial analysis has shown the project to be feasible, claims design co-ordinator and company director Mike Debens.
Impetus for the project has come from the “cash-rich” shipping industry, he says, which sees it as offering a quicker service than ocean freight and a way of overcoming constrained shipping terminal capacity.
Neither Debens nor the rest of Droneliner’s directors are engineers, but the company has been able to call on a highly experienced, independent technical advisory panel – including former Airbus chief aerodynamicist Behrooz Barzegar and John Roberts, chief engineer on the A380 programme – to drive the design forward.
Droneliner’s aircraft are uncrewed and unpressurised, allowing significant weight saving through the elimination of the systems required to support pilots and pressurisation.
Debens points out that, apart from their cockpits, the Boeing Dreamlifter and Airbus Beluga oversize freighters are both unpressurised. “What we are doing is taking the pilots away as well,” he adds.
In addition, bleed air and auxiliary power are no longer extracted from the aircraft’s engines, boosting powerplant efficiency.
The power needed to run the on-board systems is provided by batteries and wingtip- and horizontal-stabiliser-mounted electrical generators – what the company calls “wingmills”. These also trickle-charge the batteries in flight.
A single wide-fan engine such as the GE Aerospace GE9X or Rolls-Royce UltraFan, generating thrust of around 120,000lb (533kN), is considered sufficient to power the DL200, says Debens, while the larger DL350 would use two turbofans of a similar size. The DL200’s engine would also feature a boundary layer ingestion engine duct, helping to reduce drag.
Despite the huge levels of engine thrust available, initial power during the take-off roll would be supplied by banks of battery-powered drive systems sourced from the electric vehicle industry, accelerating the aircraft up to around 70kt (130km/h) before the turbofans take over.
The proposed electric motors would also be capable of regenerative braking – both recharging the batteries and eliminating the need for engine thrust-reversers, Droneliner argues.
Debens says the power available from a single engine and the electric-powered ground wheels would exceed that of a twin-engined 777F, enabling the DL200 to become airborne “slightly quicker”.
Additionally, the removal of ancillary functions from the engines should also see more thrust available: “It leaves the engine as a propulsion unit rather than as a power station,” says Debens. “It will simply offer more bang for your buck.”
While the design of the Droneliners appears futuristic, Debens argues that the company has relied on “present technologies” that have simply been employed in a novel configuration.
Or as Roberts is quoted in Droneliner’s press release: “The basic assumptions regarding weight and performance appear valid. The technology being proposed is novel in its usage but not in its basic understanding.”
Reflecting that approach, Debens says the two UK patent applications submitted by Droneliner, for unmanned air vehicles, are related to the whole-aircraft configuration rather than unique technologies.
The UK patent registry shows the date of the applications – filed in June and October last year – but provides no further detail. Droneliner also holds a trademark for the “Wingmill” – which is described as a “wingtip-mounted vortex-powered electrical generator”, the UK trademark registry reveals.
To help aid regulatory approval, Droneliner will voluntarily limit the operation of its aircraft – banning them from serving busy airports near to major population centres such as London Heathrow. Instead, it sees potential to bring back into service many of the isolated military airfields that have been retired since the Cold War ended.
But there are still enormous hurdles to overcome if either the DL200 or DL350 is ever to see the light of day. Ignoring the obvious regulatory challenges, there is also the not insubstantial question of who bankrolls the development of the aircraft. Debens estimates the cost to bring the programme to production will be “$10 billion-plus”.
Droneliner will not fund the work in isolation, however. Instead, he sees the need for a consortium of risk- and profit-sharing partners drawn from several industries: shipping and logistics, online retail, aerospace, plus financial muscle from the investment community.
He also sees potential for other aerospace companies to take an interest, particularly if there are technology overlaps: Boeing’s research into the potential for a truss-braced wing would fit neatly with Droneliner’s design concept, albeit the two use cases sit at different ends of the speed range.
“It could be something that would follow on from that project, using all that they have learned,” he says.
Droneliner will also canvas the market before it decides which design to pursue first. “It all depends on what customers want,” says Debens. “We need to get the product right.”
Besides the commercial market, Droneliner sees scope for a military variant, helping to spread the development costs. Possible missions include air-to-air refuelling, parachute dropping of containerised loads, heavy-lift transport, or even surveillance.
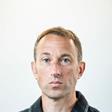